Combining Filipino expertise and Japanese technological know-how, Super Industrial Corporation designs all its products to meet the strictest specifications set by locally and internationally recognized standards. These are the PNS (Philippine National Standards); ASTM (American Society for Testing Materials); BSI (British Standard Institution); ISO (International Standards Organization); JIS (Japanese Industrial Standards)
Aside from black and galvanized steel pipes for general use in water, steam, gas, and air lines, Super Industrial Corporation also manufactures couplings, electrical conduits, and light-gauge structural. The company is also licensed to contract for hot dip galvanizing and slitting services.
Keeping pace with the latest trends in pipe making, SIC is equipped with high-frequency contact resistance/induction-welding machines in its Small Tube Mill Plant and its Medium Size Tube Mill Plant both of which can weld tube seams faster and surer than any other types.
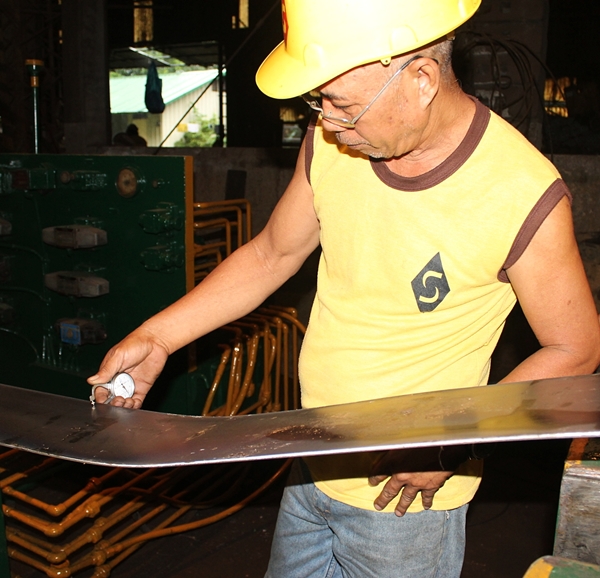
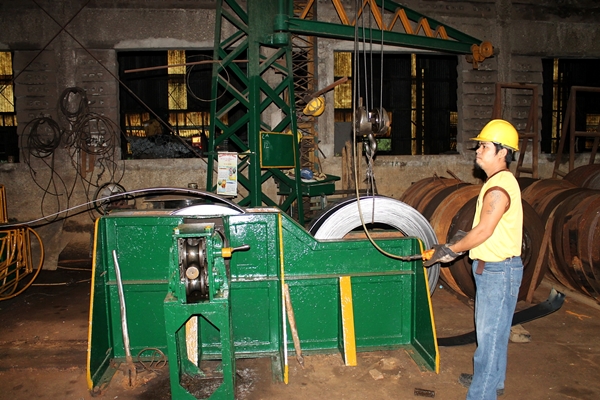
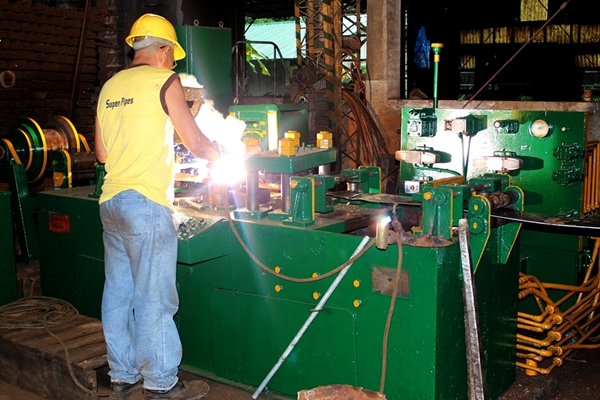
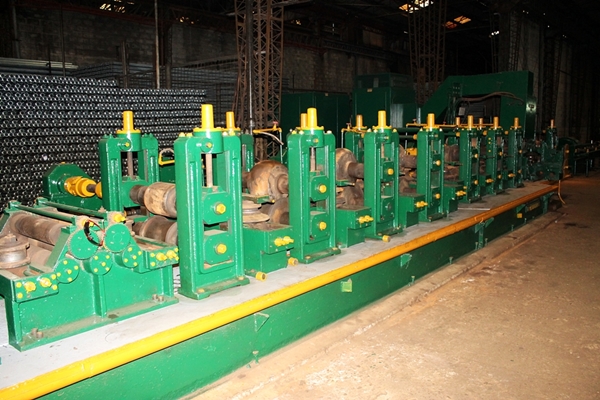

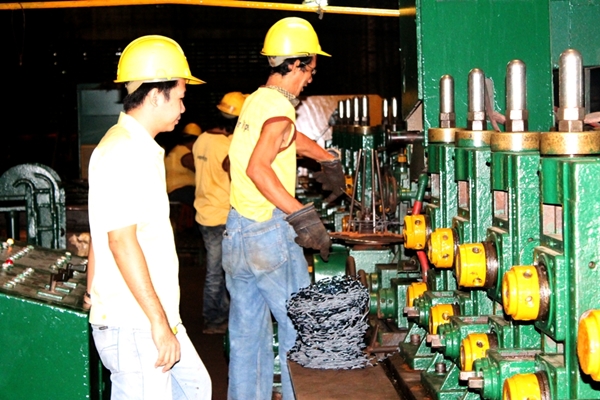
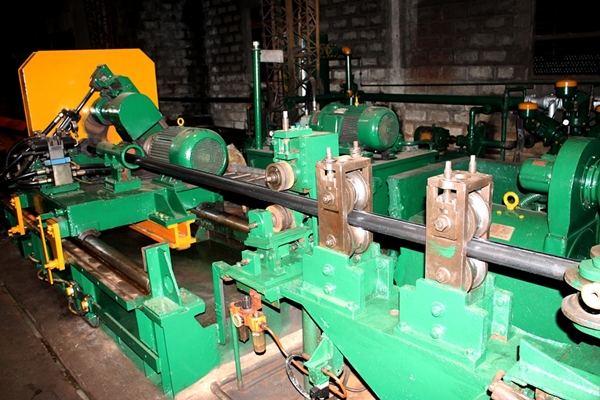
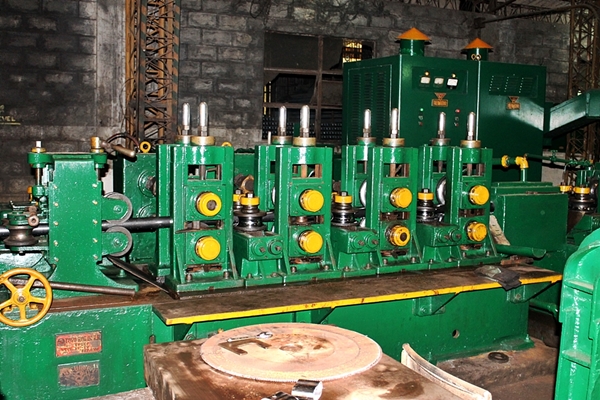
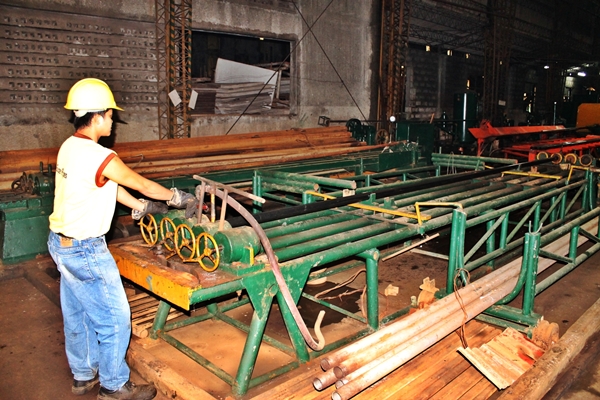
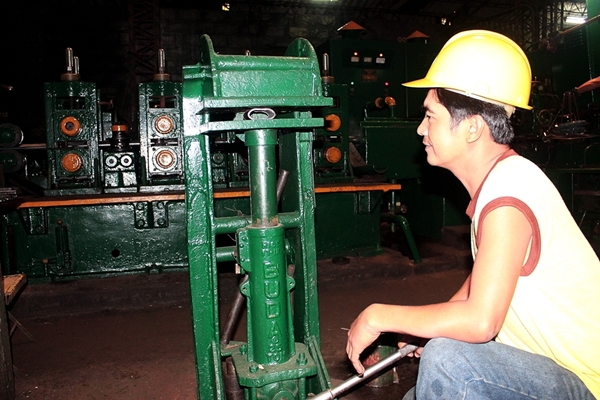
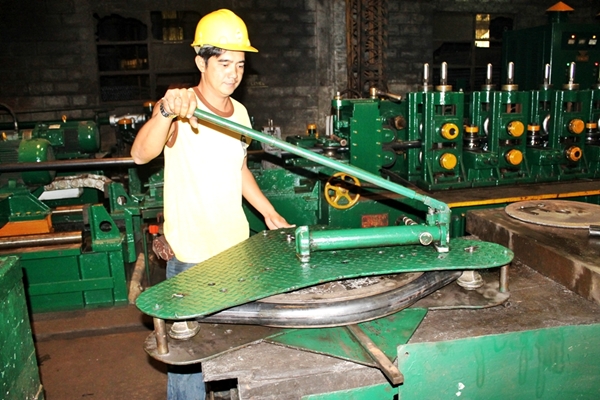
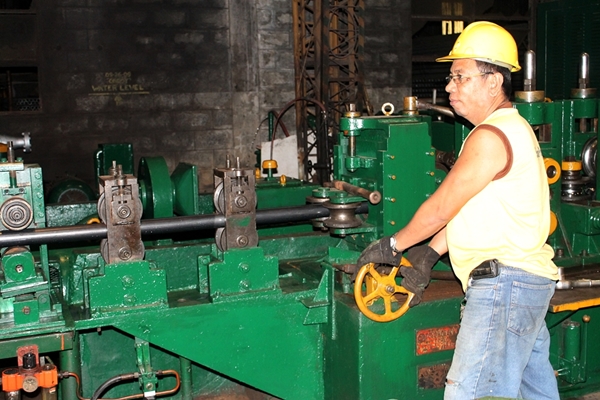
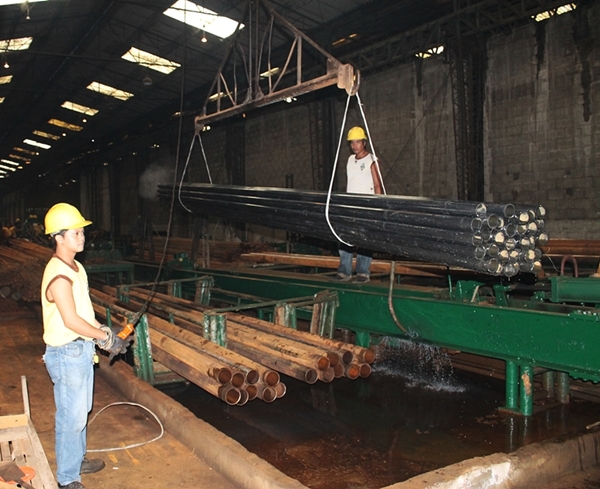
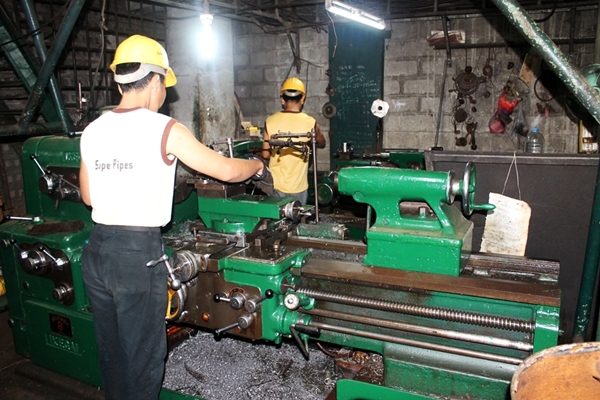
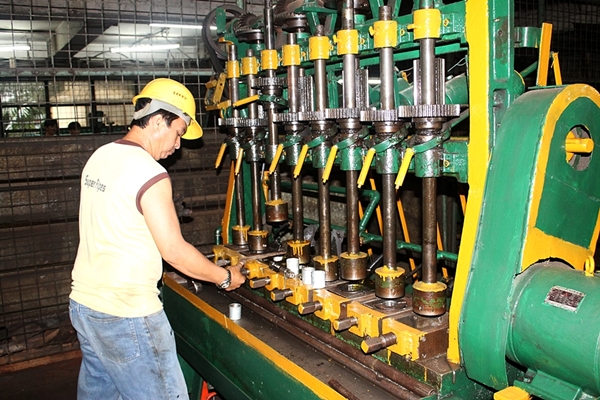
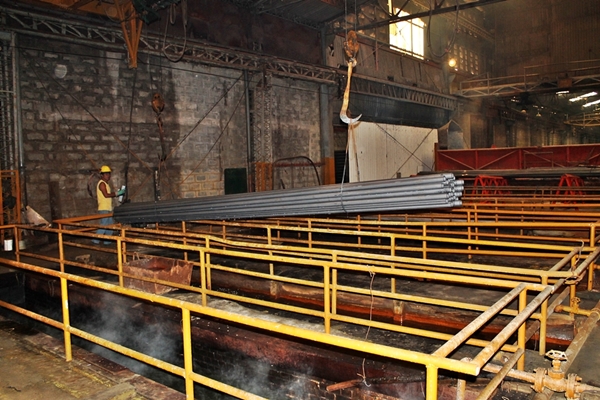
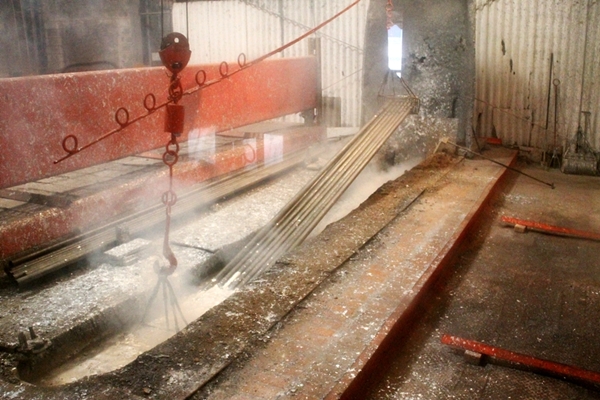
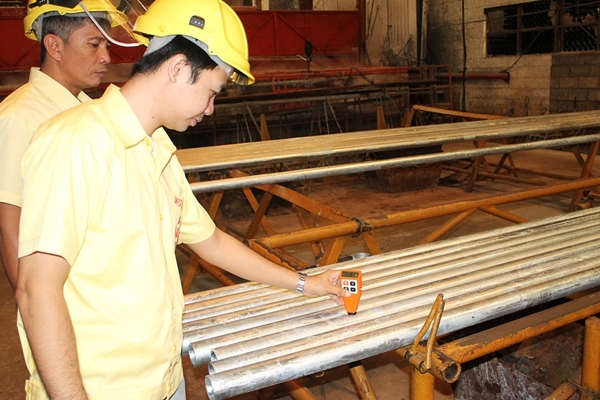
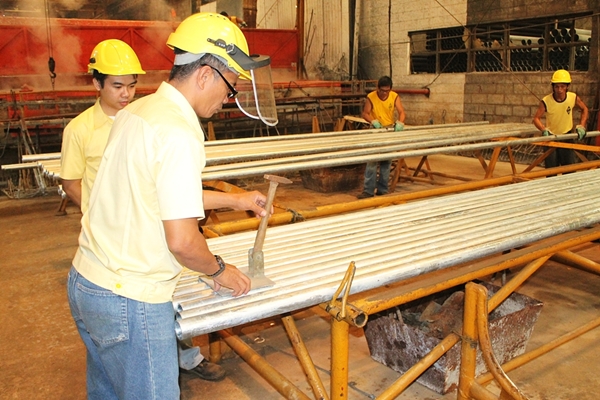
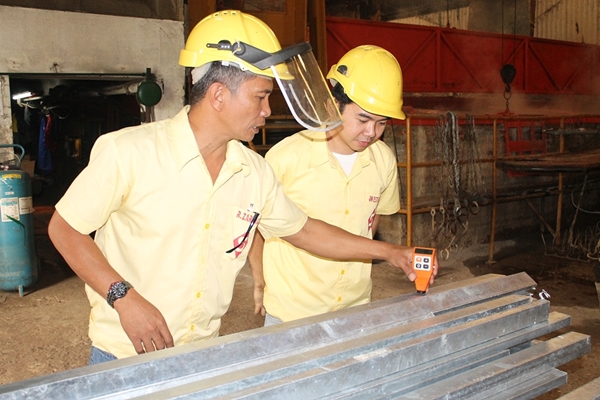
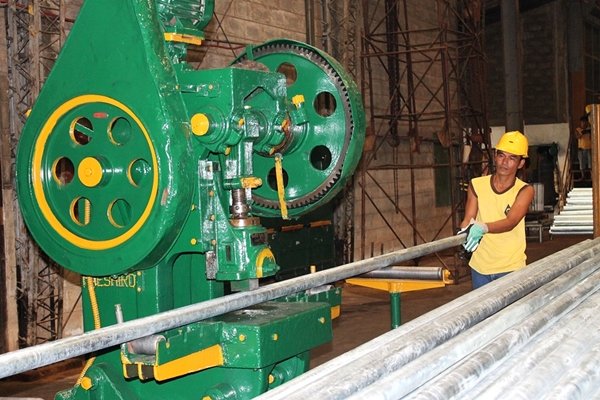
